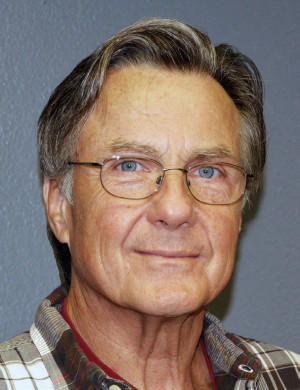
and vacuum-tube sound into a thriving amplifier
company called Raven Audio.
Shannon Becker: Tell us a little about your background and how you became interested in audio.
Dave Thomson: I have always been interested in music. I made my living as a professional touring musician and singer/songwriter for about a decade. I also have owned many different tube guitar amplifiers and loved upgrading old historic home amplifiers and receivers (e.g., Dynaco, McIntosh, Eico, Scott, Fisher and several others).
Shannon: Why are you such a huge fan of tubes?
Dave: I have always preferred the sound of tubes, but I do even more now that new technology enables it to be so much more precise, accurate, and clean. There is something very human about a great vacuum-tube based audio system.
And, there is so much more being written about them now that they are growing more popular at such a dramatic pace. Many of the negative responses you used to read were either partly or completely untrue, unimportant, or written from a clearly engineering standpoint where they completely discount or do not understand that music itself is a very imperfect, human, and emotional thing. You should always approach vacuum tube amplification with that knowledge.
People get caught up talking about perfection, precision, exactness, distortion, and a whole litany of other things that from an engineering standpoint they think is important. They relate to how precise and perfect digital and solid state can be when compared to vacuum tube audio devices. They will rant and rave about distortion until they are blue in the face, but those guys are missing the real truth about music.
They just don’t get it… very few of those guys are musicians. Not many of them are good musicians for sure! Why do you think there is a knob on every guitar amplifier that says “distortion?” There is something inherently human about slightly imperfect sound. It gives what we hear depth and realism. You can squeeze the soul right out of the music if you try to make it too perfect. It will turn sterile and the more perfect you make it, the more boring it can get. The same goes for the device playing the music. If the sonic signature of the power amplifier is too clean and perfect—the listening experience can be boring and unattractive even irritating. That is NOT what music is all about. Emotion is. It is so much easier to get up and walk away from most digital or solid-state systems than it is to get up when listening to a really great tube system playing great music. It is also why the marketing of those devices is usually filled with claims and comments like “tube sounding” or “sounds like a tube system” and so on.
So why not just get a tube system? Yeah, they can sometimes be a little troublesome. But that is precisely what tube audio is all about. Vacuum tube systems usually have more than one tube in them. And each one of those tubes can be swapped with another brand of the same or similar type. That is where tube audio really gets interesting. This is also why it can also be so darn fun!
You can find some great old tubes to install here and there that will slightly change the amplifier to better match the room or the speakers or the preamp or the cartridge or the… well you get where I am going here. That is just another thing that makes vacuum tube systems so much fun. But tubes are made of glass. Glass is imperfect — and there that word is again. They are not for everyone nor for every situation.
Tube audio takes a little work. But, I have always found that it is well worth it. You will never beat the real “human” sound of a really great tube audio system. There is no answer as to why people react to music the way they do, but striving to make it perfect and completely without distortion and imperfection will rip the soul out of the art of the performance. It would be nice if more people understood this. And I am here to try to help with that!
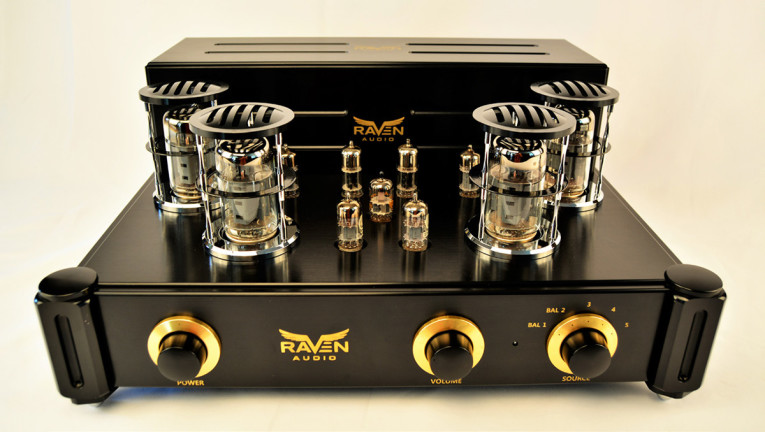
Shannon: Is that why you decided to open Raven Audio?
Dave: It all started at about 3 a.m. one sleepless night in 2010 when, while cruising the Internet looking at audio gear, I encountered the website of a well-known (in that hemisphere anyway) vacuum tube audio engineer/designer from Seoul, South Korea. I did not know who he was at the time, I just saw some pictures of his tube amplifiers. I sent him an email saying “hello from Texas, USA, nice looking amplifiers.” He immediately responded telling me that he once worked at Texas Instruments in Dallas and really missed Texas, well, let’s just say that I didn’t get much sleep that night.
A few months after that initial email exchange he was sitting in my Texas living room. When I first listened to one of his tube amplifiers, I was enthralled with the sound. I knew it was a little different than anything I had ever heard, and I had by then owned many different brands of high-end audiophile-grade products. Here in my living room was a man who had more than 48 years of experience, gained mostly through 40 years of owning one of the largest repair shops in a country where old US and European audio products are highly revered and avidly collected. He had repaired and upgraded almost every existing brand in the world, which gave him a unique window into the way all of these different designers had built their products. He also knew all the tricks and methods they used and then came up with a few of his own.
By November 2010, Raven Audio was born. I subcontracted him to design all of the products in what is now Raven Audio’s current line-up. He has since retired and now it’s time for someone else to take over where he left off. I want to bring a US engineer into the mix. Eventually, the right person will find his way to Raven Audio and will continue our work.
Shannon: Where do you get your tubes? Do you have a favorite?
Dave: I actually get my tubes from many sources, because I prefer old stock tubes. But for power tubes we have to go with what is available and the few companies that manufacture tubes today. I source our power tubes from New Sensor in New York. I will never buy Chinese tubes again.
Shannon: What was your first product?
Dave: Our first product was a version of the Reflection Integrated Stereo Amplifier. The second product was a Shadow Stereo Amplifier. Then, we developed the Shadow Preamplifier to go with it. Soon after that I asked our sub-contracted product designer to please develop a lower-priced but great-sounding alternative lineup of consumer level products that we could offer for less than $5,000. So, we came out with the Avian Series, the first model of which was the little Nighthawk. It sold for $1,995, had a manual volume, and was just a fabulous folded-steel chassis with automotive paint. That price limit was finally breached this year with the introduction of new Eagle and Golden Eagle integrated amplifiers. So now the rule is to keep it under $6,000.
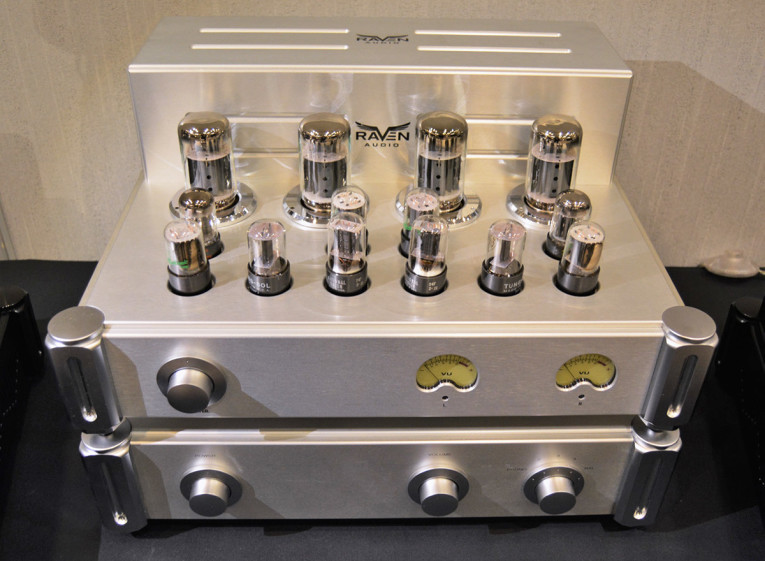

Shannon: Can you describe the main differences between your Elite Series and your Avian Series?
Dave: The Elite Series lineup are top-quality products, heavy, and expensive to build. They are all housed in thick CNC-machined anodized aluminum chassis and hand-wired using the absolute best sounding and highest quality parts in the world. Not every single part is costly, but they have to be dependable and sound great. That is where experience came into play. It’s not about which parts you use, but where you use each one of them within the circuit.
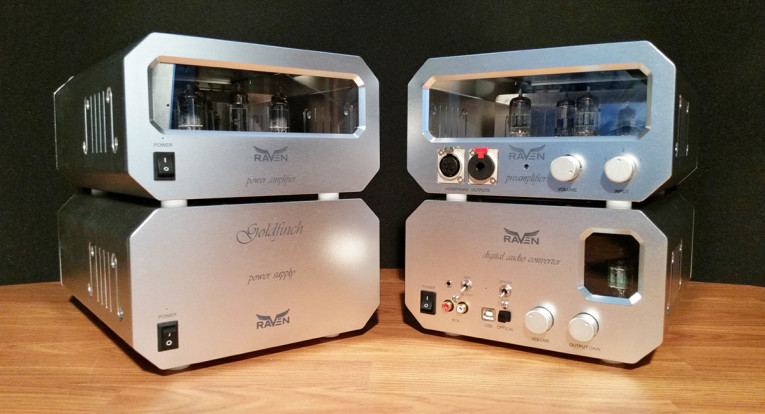
Shannon: Tell us about your Goldfinch Tabletop System. What are some of the challenges you faced? And, is it now everything you envisioned it could be?
Dave: The Goldfinch Tabletop Multicomponent Audio System is exactly what we designed it to be. It’s the ultimate high-quality, yet affordable, fantastic sounding multi-chassis system of tiny vacuum tube components. It took a long while to come up with something small that sounded like the premium top-of-the-line products out on the market. This was our goal. It just took some time for us to get it right. It’s built for small spaces, but it will also work well enough with just about any sensitive speaker system. Speakers with a sensitivity of 95 dB or higher will work very well with this system. As time goes on, there are going to be more higher-sensitivity speakers coming out as people start to get into low wattage tube amplifiers. Low-power tube amps with sensitive speakers can be a very special combination.
We have plans for a single-ended power amplifier for this system. The 8” × 12” footprint of the chassis takes up very little room, so they are perfect for small residences.
We aren’t really finished with that lineup yet. But, we already have spin-off components in the same chassis, the Cirrus Line Stage Preamplifier and the Stratus MM Phono Preamplifier. They will both have separate power supplies, and since they are more reasonably priced we hope they will become popular.
The Goldfinch Series is an entirely different world of products for small listening environments. And as cities get more crowded and space becomes a premium, and more expensive, these components will become even more important and useful in those environments.
Shannon: In addition to the preamplifiers, amplifiers, and the tabletop system, I see you also have your own line of capacitors. Can you explain why you offer Raven Audio Capacitors?
Dave: We had to make a large minimum purchase because we were in development with this contractor for such a long time trying to come up with something really special. That’s just the way it works when you ask a company to build something for you that’s new, different, hopefully special.
We approached and later hired the same company and the engineers that developed the famous “V-Cap” and some of the other more famous film capacitors, and told them we wanted to develop the best audio capacitor in the world. At first they laughed. But eventually we agreed to try, and during that quest we hit on something different that worked to make the RavenCap audio capacitor special. Along with some other technology discovered along the way, they increased the level of Teflon used in the matrix, and the addition of two other poly-components along with the use of a high-pressure injection method to force the bubbles out during the process instead of a normal “pouring” method. That, among a few other things, turned out to be the key to the difference.
The result is an almost shocking new realism that suddenly appeared when the caps built using the new method were first tested in prototype form. We knew we had something different, something really unique, something really very special. It was exciting. Once we had them, I thought it might be fun to offer some of them for sale into the DIY community.
So we put them up on our website just to get some reaction from people in the hands-on community, mainly to see if they thought it was as special as we do. But, we will only sell them for a limited time. After all… they are a large part of our unique sound. The RavenCap is also the source of the incredible punchy dampening power that all of our products possess. You can almost feel this huge deep wave when the music is played at higher levels. It makes the bass sound so clean and well-defined yet powerful.
It almost clings to the floor forming a deep layer that flows across the room at lightning speed… it’s really something. The music literally jumps out of the speakers — and so effortlessly. It also cleans up the bloat that can plague some tube audio designs allowing the music to flow so “free and easy,” almost completely without restriction, haze or veils. It’s kind of amazing. I cannot say enough about those really wonderful capacitors, except that they are a game-changer.
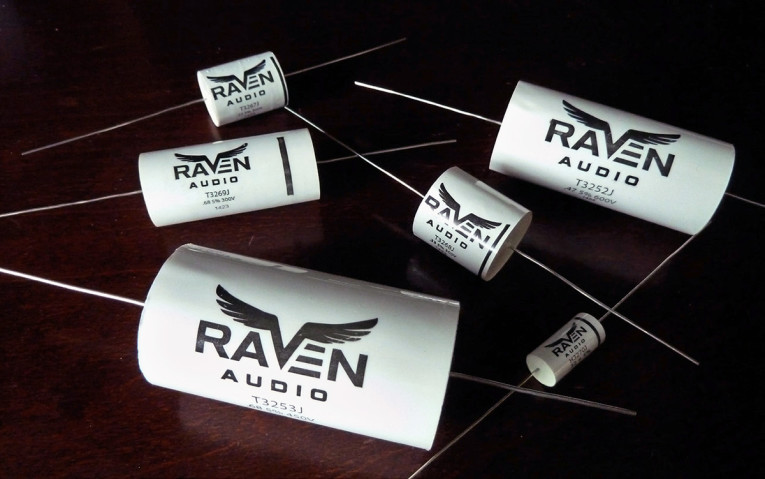
Dave: Yes we have a lot of changes coming. We were already in the process of moving into a new much larger facility due to increased demand for our products when things started to change even more. During the move, demand kept increasing, so we had to stand back and make a few decisions or it looked like we might outgrow our new facility before we even get fully moved in.
We had originally planned to move in and set up our own manufacturing shop and have two separate manufacturing areas in the same building. One side would be set up to build the Avian Series products, which are our PC board based integrated amplifiers, and the other side would house the Elite Series manufacturing area, where all of the CNC-machined aluminum, hand-wired point-to-point would be built. The Avian Series started selling so fast that we decided to take the Avian Series to an already existing highly specialized electronics manufacturing facility in College Station, TX. This move will enable Raven Audio to build more than 100 units per month.
The main thing is that our customers will never again have to place an order and wait for their amplifier. The plan is that we will keep several of each model in stock, and each purchase will trigger an immediate replacement to be built. Every week stock will be sent to over and stored at the shipping facility in Trinity, TX, ready to send out at a moment’s notice.
The Avian Series line are all similarly housed in folded steel chassis with aluminum face plates and have a separate raised aluminum preamp plate on top. The existing Nighthawk MK2.1, the Blackhawk LE, and the Osprey all have handles and weigh in at about 40 lb. and are in the same basic steel chassis. The newest members of the Avian Series — the Eagle and Golden Eagle — are coming out in 2017 and are much larger, about 60 lb. each. They are heavy and must be handled from the bottom sides of the chassis, and for now the Eagles look really nice as they are, and they are safe to carry this way.
Now, the new Onalaska shop will be dedicated completely to the manufacture of the Elite Series, our all machined-aluminum, point-to-point, hand-wired product line. So, expect some really exciting changes in the coming years from Raven Audio.
Shannon: You also took on some new business partners. Can you elaborate?
Dave: The new partners are all previous customers of either us or Legacy Audio. Tim and Connie Qualls are old friends… Tim is a fabulous drummer of some note and has had a long love affair with vacuum tube audio, mainly guitar amps. Connie is a long-time small business owner.
Marc and Kyle Trotter are a father and son active investment team, and Marc just retired from a long history in sales at Bristol Myers Squibb. Marc will work with Raven Audio and help us at the store and the audio shows. Kyle will help us with the business growth planning and documentation. Our new partners came to us through osmosis and offered their help due to their extreme love of high-end audio and a desire to see Raven Audio succeed!
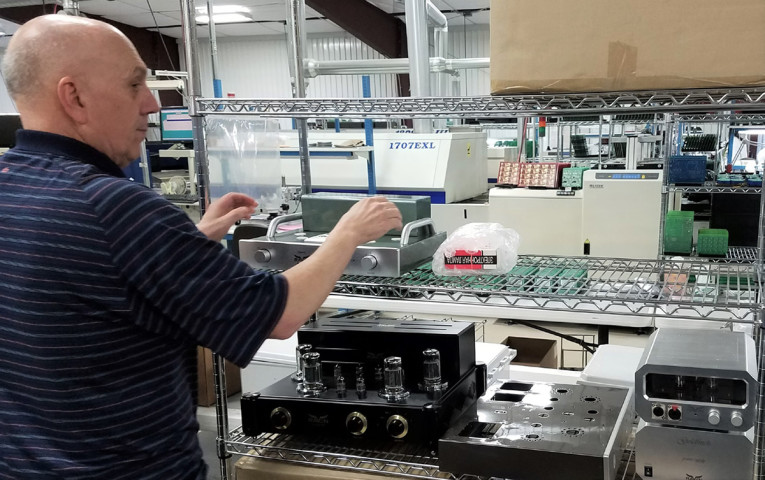
Dave: The new store is in Onalaska on Lake Livingston, which is about 100 miles north of Houston. We are distributors for Legacy Audio, Mytek Digital DACs, Douglas connection cables, and we are also bringing in Emotiva home-theater amplifiers and JVC projectors in the near future.
We have a perfect home-theater room, three two-channel listening spaces, a nice little office, a decent sized manufacturing room, and an additional room for box storage, burn-in and packaging. There are also two smaller satellite rooms that currently house a little photography studio and a bedroom. For the short future we plan to stay here because it is kind of a perfect location. It is only 15 miles from the original home of Raven Audio “La RanChita” in Chita, TX.
Shannon: Since you parted company with your original designer, can you tell us your plans for the future?
Dave: For now, we are employing two part-time electronics engineers. We also have access to several in-house engineers in College Station and have an open position for a full-time vacuum tube audio designer. We are good for now, but are taking applications for the right person.
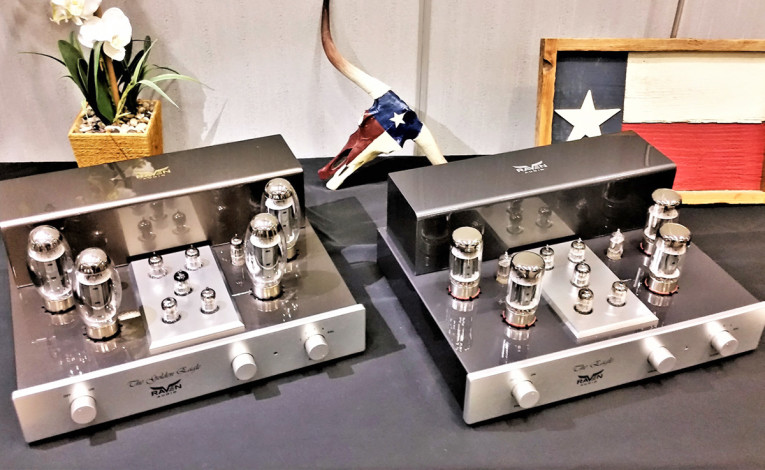
Shannon: What can we expect to see from the Raven Audio this year?
Dave: For 2017, we are officially rolling out the Eagle and Golden Eagle, which are the final members of our Avian Series integrated amplifiers. The Eagle will be able to use any power tube in the 6550/KT88 lineup (e.g., the KT88-90-100-150) and each different power tube choice can really change the sonic signature of the amplifier in both the sound and power output.
The Eagle will be formally rated at 50 W per channel. Of course, this will vary slightly according to each tube quad chosen. The Golden Eagle will use only the KT150 tubes and is rated at 75 W per channel, but the KT150 is able to bring up to and even over 83 W per channel when using its full potential. It’s the most powerful octal base beam pentode power tube out there currently. ax
www.ravenaudio.com
This article was originally published in audioXpress, June 2017.