Wood and MDF vs. Plastic
Wood and wood particle board cabinets are traditionally used for mid-to-large-size speaker enclosures. Other materials have been tried with limited acceptance but that has begun to change in a big way and is the focus of this article. Most bookshelf and larger boxes are simply medium-density fiberboard (MDF) that is vinyl wrap-covered and “groove folded” out of a larger sheet (see Photo 1). The grove-folding process cuts a V-groove into the wood, down to, but not through, the vinyl covering. A bead of glue is dispensed into the V-groove and the enclosure is miter-folded into a box shape. Conventional particleboard boxes are inexpensive, readily available, and a known commodity.
Most of us acknowledge that the typical MDF has good acoustical qualities, but curved and shaped parts with this type of construction add greatly to the cost, along with the weight and bulk of MDF thick-wall construction. MDF just does not lend itself to thin unobtrusive soundbars, let alone smart speakers or in-wall speakers.
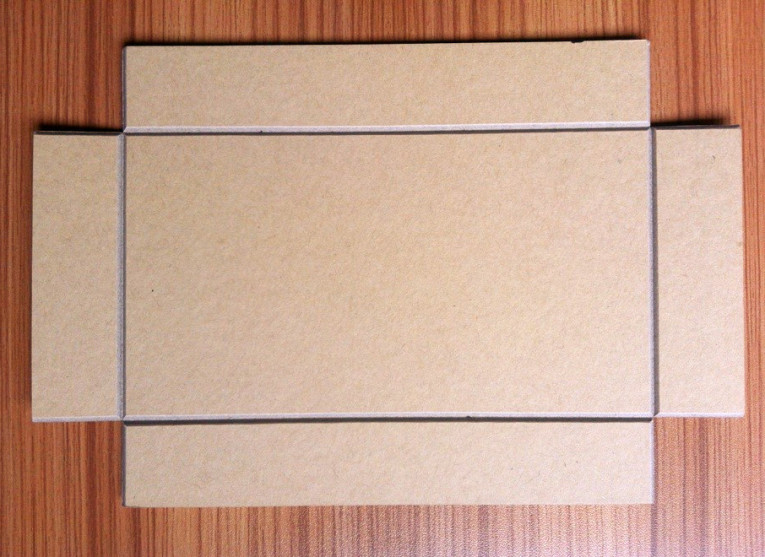
But wood boxes have their limitations. The sharp baffle edges diffract sound where it is not wanted. The flat baffle with the woofer and tweeter directly mounted in the same plane means the acoustic centers are most likely not aligned, and perhaps most importantly, your box will look just like the other models on the sales floor. How can you blame the customer for assuming little thought was spent on engineering if the exterior appearance gives this impression?
Back in the 1970s, you could walk into an audio specialist retailer and not find a single audio product with a plastic enclosure, at least not with a speaker built into it. Plastic construction was for kids’ toys, walkie-talkies, and portable “transistor” radios, but not for music reproduction. There were various reasons — one being that at the time, plastic tooling costs for serious audio products could not be amortized by the product sales numbers.
Now consumer audio electronics are mainstream and global, and the quantities are huge. The days of the US union machine shop and hand work tooling on a lathe are history. Today, tooling is done on computer numerical control (CNC) machines directly from the 3D CAD in China, from very efficient specialists and the costs are reasonable.
The other part of the reality was that “plastic stuff” in the old days did not fit in with a boutique audio retailer’s ambience. Even the little KLH table radio that was popular in the 1970s featured veneered walnut, Fisher or Kenwood stereo receivers were displayed at audio retail stores with their optional wood cases and typically bundled with groove-folded 5/8” thick particle board speaker enclosures with wood-grain-looking vinyl wrapping.
Today, take a trip to the Apple store and you will see wall-to-wall plastic (aside from Apple’s iconic machined aluminum products) and there is more of the same plastic at Best Buy — you would think wood was the non-renewable resource in dwindling supply, not petroleum-based plastic products. In the late 1990s, high-end wood grain and black lacquered speakers reappeared because of the establishment of quality wood speaker enclosure factories in China. Today, most (but not all) of the Chinese woodworking shops have done one of three things: expanded into other businesses (e.g., furniture for luxury hotels and retail store display furniture for high-grade products), found other endeavors altogether, or closed.
Several factors have driven these firms away from high-end speaker enclosure work including the atrophying of the global audiophile market, wage costs for such labor intensive and time-consuming work, and loss of interest of Chinese workers in such tough and arduous jobs.
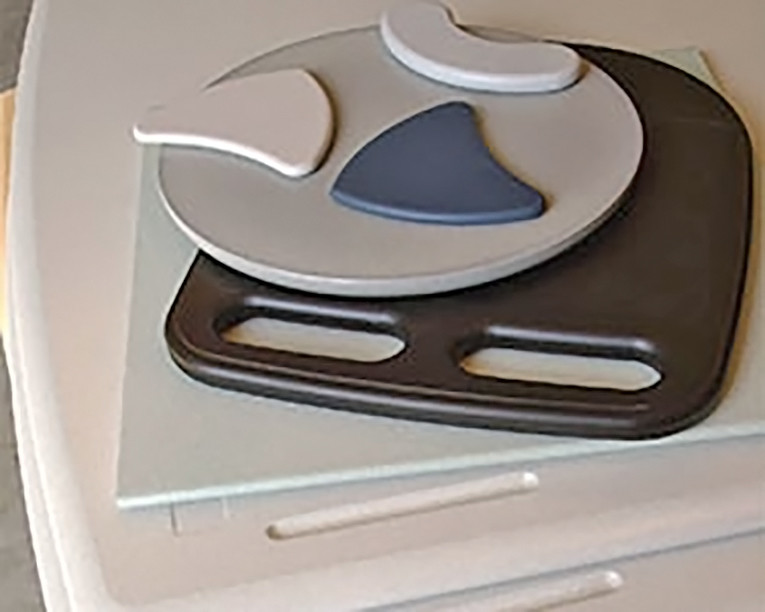
Innovations
While wood is the incumbent and real-wood veneers are expensive and particle board with vinyl wrap with fake wood grain has become just too tacky, are there any other finishes? Over the years, numerous techniques were introduced to revolutionize the speaker enclosure business, but not all of them are practical.
In the mid-1990s, Cubicon used recycled paper and fabricated enclosure tubes with fancy finishes (as well as carpet coverings for the autosound aftermarket). These tubes were square, round, D-shaped (autosound), and trapezoid (discomobile). The multi-layered paper/resin composite offered a well-damped material for enclosures and the radiused edges minimized diffraction effects. But, the tube shape tolerances were not consistent enough for mass production. End cap fittings were problematic, although a few firms managed to devise workable production techniques. In any case, while recycled materials are “in,” you won’t see many speaker enclosures made from recycled cardboard tubes these days, although soundbars might benefit from this approach.
A more sophisticated honeycomb technique was used in Celestion’s SL600. Introduced in the mid-1980s, the speaker enclosure used a rigid honeycomb alloy called Aerolam instead of wood. Honeycomb had its advantages, but attaching drivers, joining panels, and sound breakthroughs were problems not easily or inexpensively resolved. One innovation for MDF speaker enclosures that struggled but now is finally viable is powder-coated wood (see Photo 2). Powder coating enables rounded corners and contoured edges, while other lamination techniques that rely on edge-banding methods cannot. Powder application is a one-step finishing process, not requiring successive coats or long drying times. Powder coating offers a seamless finish and protects MDF products from chips, stains, spills, and scratches.
Unlike vinyl wrap, the finish is genuine, not fake wood. Since the 1960s, powder coating has revolutionized the finishing industry by providing a durable, environmentally friendly finish, particularly for metal products (e.g., appliances, automotive parts, autosound speaker frames, and outdoor metal speakers). Technological advancements in application and curing methods have also brought the advantages of powder coating to heat sensitive substrates (e.g., particle board).
MDF initially seemed suitable for powder coating because of its low porosity and homogeneous surface, but many issues surfaced with the process 20 years ago. Today, the more competent wood powder coaters have the ability to cut and prepare the MDF for coating in-house, which is critical because moisture content must be tightly controlled by minimizing the time between cutting and coating. While a detailed explanation is beyond the scope of this article, the key takeaways are that the materials and an understanding of the process have been refined. Yet the process, even today, varies among manufacturers, with some using thermal-only production, some use UV-only production, and some using a blend of both.
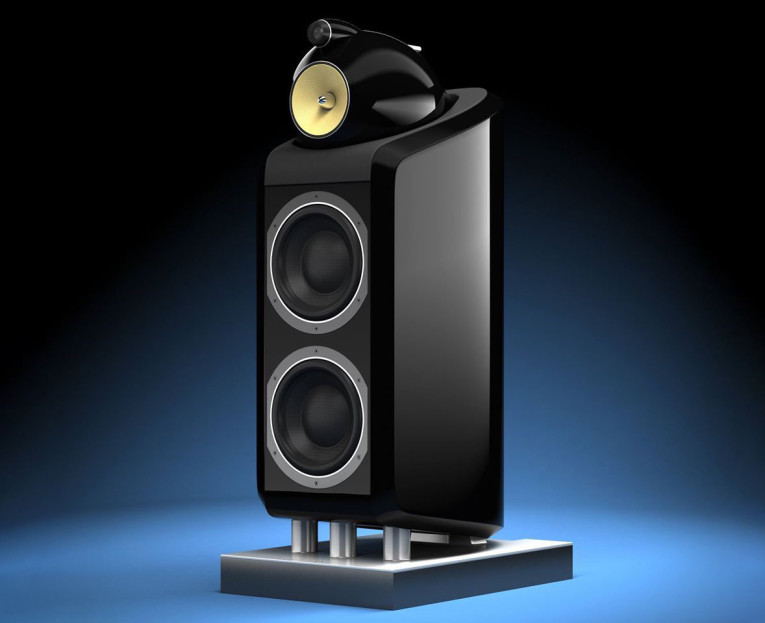
Other Alternatives
Over the years, there has been great interest in finding alternatives to wood enclosures. The ideal material should be as strong, light, and thin as plywood, and as easy to work with as particleboard. Simplified construction is another consideration (e.g., moldable materials that eliminate joint assembly and enable rounded edges and shaped front baffles for time alignment, waveguides, and esthetic flexibility).
Dramatic enclosure styling that combines unique materials and forms takes engineering and marketing courage, but the rewards can be great. Out-of-the-box implementations (sorry for the pun) such as the five-sided Bose 901 launched in 1968 and Bowers & Wilkins’ (B&W) distinctive Nautilus 800 series (see Photo 3) were breakthrough designs in the late 1990s.
The Bang & Olufsen (B&O) Beolab 5 and the B&W Zeppelin Air iconic looks enhanced their companies’ brand recognition. The usual injection-molded plastic thin-wall construction found in today’s in-wall speakers or low-cost home theater systems are marginally adequate for commodity consumer speakers. Most speaker engineers are unhappy with the hollow “buzzy” sound that comes from plastic speaker enclosures. Yet why do injection-molded plastics dominate audio these days?
Is it that stylish shapes and consistency are readily achieved with an established supply chain and well known design rules? I have mentioned that sharp edges cause diffraction, specifically the edge of the cabinet acts as a second sound source, destructively interfering with the original signal. To achieve an optimum engineered design for a more precise or “focused” soundstage, the drivers’ acoustic centers should be mechanically aligned, which is especially beneficial in the vicinity of the crossover frequency. The molding of a tweeter horn/waveguide is a useful tool to control directivity, increase sensitivity, and provide for the time alignment of the acoustic centers of the woofer and tweeter in the transition crossover band.
Wearables from headphones and earphones to smartwatches all rely on injection-molded parts for their structures. Yet injection-molded products of plastic are still perceived as “cheap” and have mediocre acoustic characteristics. The popular Bluetooth speaker enclosure panels resonate and whatever bass that can be eked out of small speakers is further reduced through losses by enclosure “barrel” flexing. Put in a hefty amplifier, some needed bass EQ, and a decent speaker, and the plastic enclosure will just rattle louder.
From the most inexpensive styrene to mid-grade ABS, plastic enclosures have high levels of breakthrough. This is the speaker’s backwave sound energy passing right through the enclosure shell and is measured as in building construction room-to-room isolation acoustics as sound transmission loss (STL). Higher sound transmission loss is the measure of how good a barrier the enclosure is to prevent sound from passing outside the enclosure. When driven hard, cheap plastics contribute too much of their own “self-noise” (rattle resonances and creaking stress noise), further degrading sound quality, the “acoustic aesthetics.” None of this is news to experienced speaker designers. However, there are plastics that we will discuss here that are much better behaved.
Yet beyond the acoustic aesthetics, the integration of electronics with the mics and speakers makes the enclosure shakes an even more serious consideration. Let’s look at how enclosure resonances degrade the full duplex acoustic echo cancelation (AEC) performance when speakers and mics inhabit the same enclosure housing. High Q break-up modes in the enclosure are excited by the speaker and the peaks set off panel resonances, which trigger the AEC running out of margin. A comparable issue is acoustic feedback where the enclosure contributes to the speaker system’s peaky response and those peaks trigger acoustic feedback. Drop the Q of the peaks through more heroic ribbing in the right spots and/or more highly damped materials and this enables more gain before feedback. For injection-molded products that are already tooled, the obvious solution is a more acoustically damped injection material.
Wood-Plastic Bio-Plastics
Mixing milled wood (wood flour) with thermoset resin in medium wall thickness cast products has been used successfully in speaker products. Wall construction is a bit thick, casting time can be 10 minutes or more, and there tends to be significant secondary finishing operations — which relegate this process from short to medium production runs of mid-to-high price products. Acoustically, these types of constructions are quite good but not practical options for mainstream products.
Converting polyester resin compression molded/cast processes to be able to use existing injection molds has been an elusive development process. In 1907, Leo Baekeland invented Bakelite, a phenolic resin to which he later added wood flour to produce a wood plastic composite gearshift knob for a 1917 Rolls Royce. In the 1970s, wood flour gained limited acceptance as a functional filler for thermoset resins (e.g., melamine and phenolic) for high-heat automotive and appliance products. In the 1980s, thermoplastics such as polypropylene (PP) with wood flour found applications. If you have a premium car, the “wood” in the interior may be wood flour plastic composite with a photographic transfer wood grain skin.
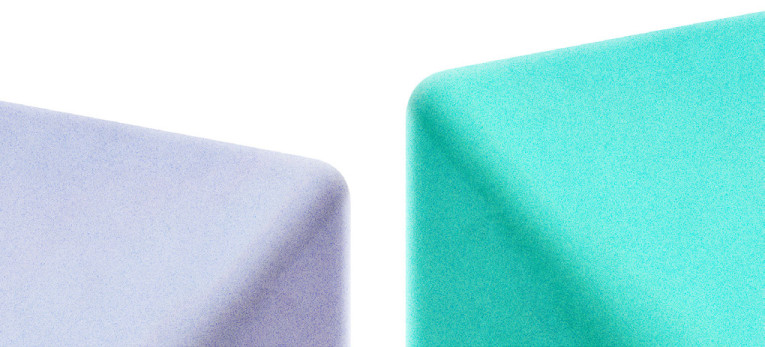
Symbio
Sappi is a leading diversified wood-fiber group, focused on dissolving wood pulp, paper pulp, and paper-based solutions. Sappi invented a new cellulose reinforced polypropylene composite consisting of virgin polypropylene and treated cellulose called Symbio. Sappi’s Symbio is available as granules for injection molding from 20% to 40% cellulose. Shrink/spring back is also minimal so the injected molded parts net shape is much closer to the tool shape, ideal for new tooling but depending on what plastic the existing tooling was “tuned” for, may require some tweaking.
Since Symbio has less shrink, this enables deep ribs without sink marks and much thicker walls in product designs. It is even possible to injection mold a subwoofer enclosure from medium wall Symbio. Fibers come from sustainable and controlled sources, available as FSC- or PEFC certified. Symbio PP can be reground, recycled, or burned for energy. Pricing of Symbio is a modest premium over basic polypropylene and ABS. Like other thermoplastics, Symbio can be compounded with color so painting is not required.
Yet higher-grade consumer products require painting — and quality paint finishes can cost as much or more than the plastic enclosure itself. Sappi has also introduced Vivid, an enhanced molded-in texture soft touch finish (see Photo 4). Sappi’s Vivid is in the early stages of development and provides the qualities of standard Symbio and adds unique visual depth and texture of rubber paint with a warm touch.
Eastman is an established and leading plastic resin supplier that offers TREVA, a cellulose-based (bio-based content of 42%) engineering bioplastic, which offers both high acoustic (superior damping) performance and reduced environmental impact. TREVA is chemically resistant, dimensionally stable and has excellent flow, and BPA-free.
In Part 2, we will explore more fully the range of enhanced thermoplastic resins, thermoplastic, and thermoset composites, including with carbon fiber reinforcements and bulk and sheet molded compounds. We will also take a deeper look into their applications for audio housings. VC
Read Part 2 of this article here.
This article was originally published in Voice Coil, March 2019.