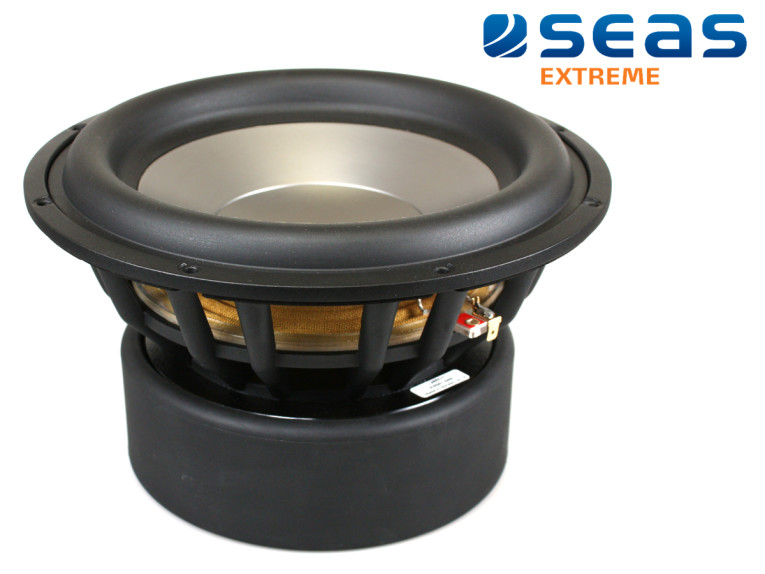
The Extreme subwoofer series is a new in-house manufactured successor to the highly acclaimed SEAS Design series of subwoofers, for now with two models. The XM001-04 is a drop-in replacement of the D1001-04S L26ROY which was launched in the Summer 2018, while the new XM004-04 is a drop-in replacement for the D1004-04S L26ROY, which is the version with 4-layer voice coil, suitable for vented boxes and open baffle application.
The SEAS Design product line was introduced in 2009 and quickly rose to fame for providing an extremely accurate subwoofer reproduction, and having been applied in various high-end products in closed boxes, vented boxes, transmission lines and open baffle designs, as well as the venerable High-Performance Do-It-Yourself (DIY) kit named the Linkwitz LX521. These subwoofers were designed with the best possible linearity, not only considering the classical force-factor and compliance linearities, but also balancing reluctance forces, for lowest possible overall distortion in the most demanding high-excursion subwoofer application.
The new Extreme subwoofers continue the brands’ tradition of targeting the best performance in its drivers, now with a new design and manufactured directly at the SEAS own production facilities in Norway. SEAS has made a video available of the pilot production here.
The updated basket design is optimized to reduce airflow noise, with more smaller spokes, while the speaker features the brand’s Spider-Ring-Assembly (also made in-house) and 6.3 mm gold plated terminal spades, suitable for snap-on connectors and also for soldering. Several small upgrades that both improve overall performance and allow the new subwoofers to be drop-in replacement for the Design-series.
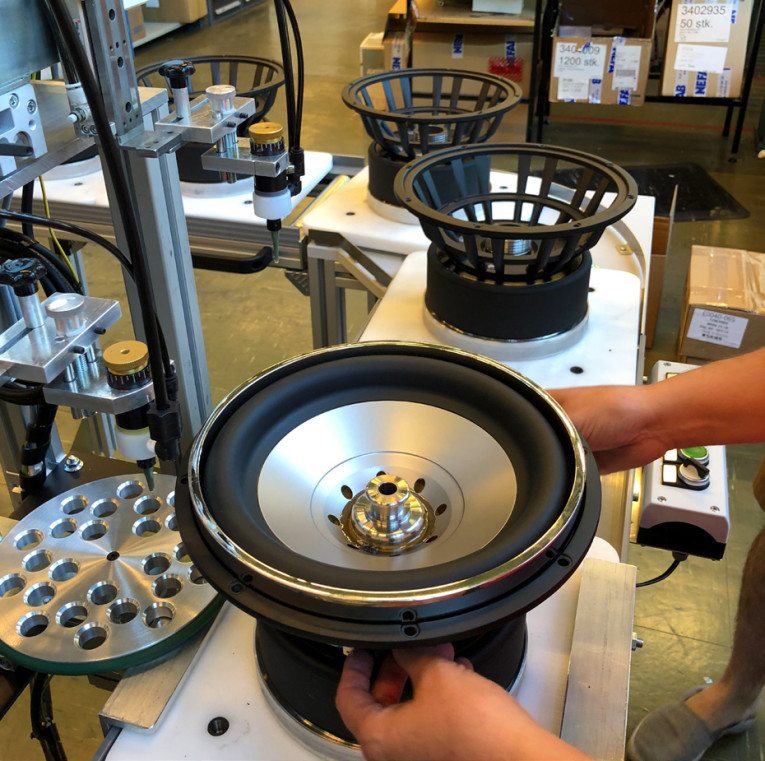
The basket design in the new Extreme family was optimized to reduce airflow noise for low frequencies, enabling a huge improvement in open baffle applications. Large windows in the basket, both above and below the spider, reduce sound reflection, air flow noise and cavity resonance to a minimum.
The new XM001-04 L26ROY uses an extremely stiff and rigid aluminum cone, which together with a long throw low loss rubber surround show contribute to extreme bass precision, with no signs of the familiar cone edge resonance and distortion associated with soft cones. The lead-out wires are symetrically stitched to the spider to avoid resonances and total suspension assures stability for extreme excursions.
A 2-layer, extremely long, high temperature voice coil wound on a glass fiber voice coil former gives it a high power handling capacity. Cu-cap around the pole pieces reduce non linear and modulation distortion and increase overload margin, and an extra large magnet system provides high efficiency and low Q. Finally, an extremely stiff and stable injection moulded metal basket keeps the critical components in perfect alignment.
As for the new XM004-04 L26RO4Y, this has been featured also with an extremely stiff and rigid aluminum cone for improved bass, using the same type of cone and the long throw low loss rubber surround, lead-out wires symmetrically stitched to the spider to avoid resonances and total suspension for extreme excursions. The differentiation lies in the 4-layer, extremely long, high temperature voice coil wound on a titanium voice coil former, which gives it a high power handling capacity. Cu-cap around the pole pieces reduce non linear and modulation distortion and increase overload margin and an extra large magnet system provides high efficiency and low Q.
From a pure cosmetic design perspective, the magnets in the Extreme series are now covered with a smoother designed rubber boot. The packaging material is also improved with sturdy foam in cardboard boxes.

SEAS Fabrikker, celebrating its 70th anniversary in the audio industry, is investing to revitalize and improve all transducer products, quality control and manufacturing for the future, improving reliability, quality, and flexibility. Many developments have been in preparation for years, while SEAS Fabrikker has moved part of its manufacturing from Taiwan to Norway, and now introduced the refreshed Extreme series of subwoofers.
The Design series drivers were launched 10 years ago, in 2008, and are quite popular with listeners of the Siegfried Linkwitz’s design Orion and LX521. It stands for one of the best subwoofers on the market today. And, it is remarkable that many high-end designs use these dedicated 10” subwoofers up to about 150 Hz to 200 Hz (depending on the steepness of the crossover) with clean results. The main reason for the decision, to move the production in-house, was precisely to improve flexibility with regards to OEM customization of the subwoofer driver range, with color and impedance options, in a way like its other products.
The company now can manufacture and supply these drivers much quicker than before (shorter lead time), which is part of its customer experience of SEAS as a flexible and reliable business partner. SEAS now also offers complete subwoofer system solutions with amplifier and cell phone app. control for assembly in Moss, Norway. SEAS is manufacturing the “Pandora” subwoofer (see photo), which is readily available to ship to interested parties. As the company states, “It was always part of the SEAS business plan to offer turn-key products and we continue to service our customers this way.”
The new production setup is organized on a classical oval production-line, to ensure that employees don’t have to lift the heavy woofers at any time. Norwegian labor law requires that employees do not lift anything heavier than 7 kg in their arms, so from assembly of magnet system and onwards it’s a classical stack-up process. Besides, SEAS utilizes the special Spider-Ring-Assembly (SRA) technology, known from other SEAS products, where a ring (with terminals) is used for assembling all the soft parts, including electrical termination, so that the soft parts can simply be dropped into the basket on the production line. All the details, including length of lead wires and soldering, is handled on a separate round-table before entering the production line. This ensures a better flow (easier, more predictable, with fewer steps) on the production line.
The entire production line including the PLC controllers, and associated SRA assembly station and production tools were designed and developed in-house (and to a large extent also manufactured in-house). The company only purchased the components from suppliers.

As SEAS also confirms, all the product design and in-house production improvements will allow OEM clients to benefit from customization enhancements with shorter lead times. As an example, SEAS details available OEM production batches - minimum 100 units - with black cones, Titanium voice coil formers, 8 ohm impedance, etc.
www.seas.no